Sea Change | Texas Monthly | May 2021
Alongside the Brownsville Ship Channel, which shoots straight as a drill bit into the Gulf of Mexico, one of the biggest manufacturers of offshore oil rigs on the Gulf Coast turned 180 acres of dirt into a veritable gold mine. The shipyard there is a maze of 43 buildings, including 7 hangar-size assembly sheds in which welders’ sparks fly, pneumatic hammers pop, and signs warn in bold letters that any misstep could maim. Into one end of the factory slides sheet after three-ton sheet of steel. Out the other end, like intricate toys from some gargantuan Santa’s workshop, roll some of the heaviest and most sophisticated pieces of energy-industry machinery in the world.
During an extraordinary oil boom at the outset of the twenty-first century, the yard cranked out a steady stream of “jack-up rigs.” As tall as skyscrapers, these offshore platforms tap petroleum miles beneath the ocean floor and fetch about $250 million apiece. Five years ago the yard birthed a 21-story-tall beast called the Krechet, then the largest-ever land-based oil-drilling rig. But the Krechet—Russian for “gyrfalcon,” the largest falcon species and a predator of the Arctic tundra—has proved something of a dinosaur. Now pulling up oil for Irving-based ExxonMobil and its partners in Sakhalin, an island off Russia, it’s likely the last such oil rig the shipyard will ever build.
Today, in a pivot that reflects an oil-and-gas industry transformation sweeping Texas and the globe, the Brownsville yard’s workers are fabricating a new sort of ship. Like the old-style oil rigs, this offshore-energy vessel will head out to sea, lower its hulking steel legs onto the ocean floor, jack itself up on those haunches until it straddles the water’s choppy surface, and, in a dance of power and precision, drop into the murky depths machinery that will penetrate the subsea rock. This time, though, the natural resource the ship seeks to exploit isn’t oil. It’s wind.
Read more here.
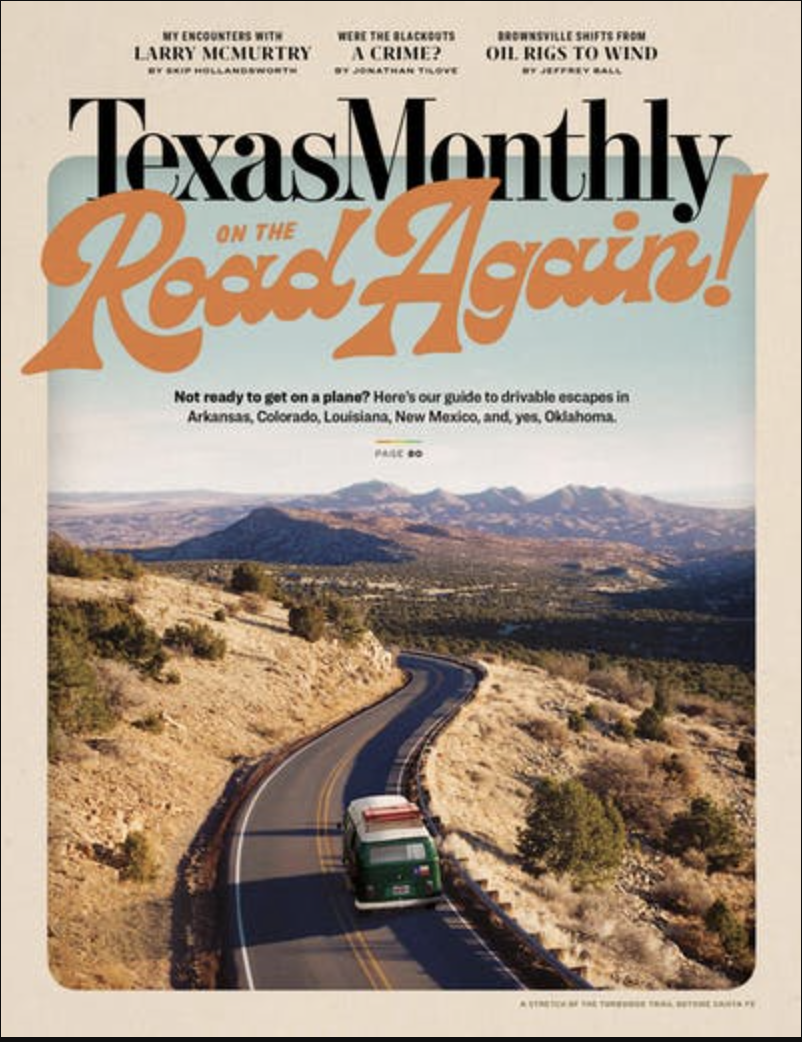